What Are the Risks of Not Calibrating?
Calibration is used to determine the parallel between the input and measured output the instrument is measuring under specific conditions.
A calibrated instrument ensures the equipment is working within its correct specifications and provides accurate measurements. These measurements are then quickly and easily documented, which is essential for companies complying with ISO 9001 standards, which are overseen by regulatory bodies that need to know how accurate or inaccurate an instrument is and whether it operates in or out of its specified tolerance.
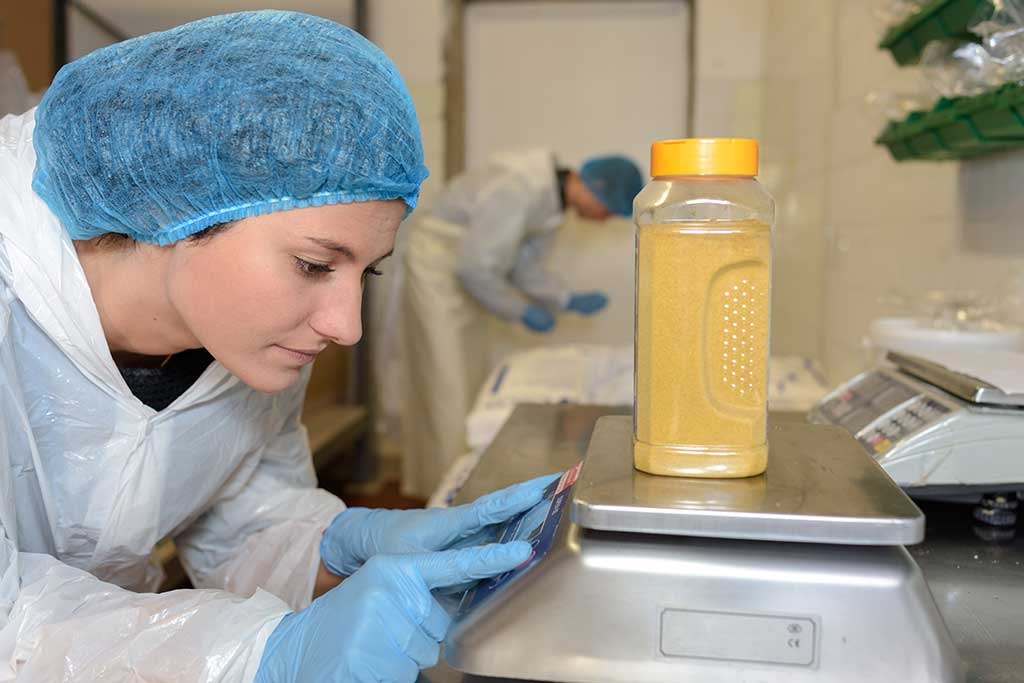
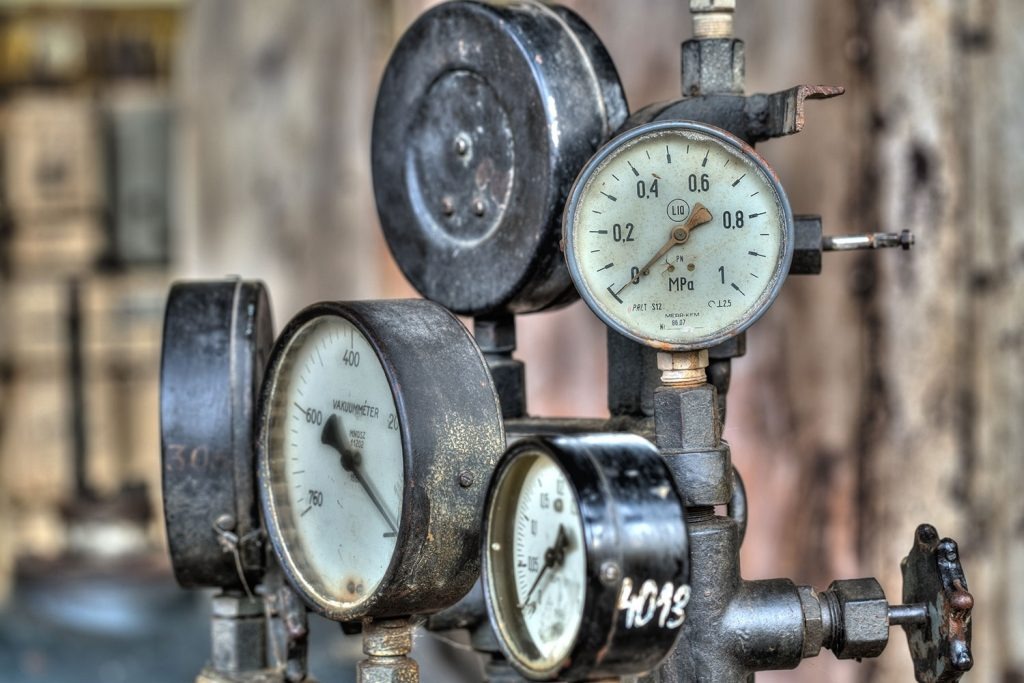
When to Calibrate
In general terms you should get your instruments calibrated when:
- They Are New
- Once a specified period or a specified number of operating hours has elapsed
- The device suffered an unexpected shock or vibration that may have put it out of its specified limits
The Importance of Calibration in Industrial Processes
In industrial applications, sensors and instruments can experience extreme temperature variations and physical stress. These conditions can, over time, cause a decline in performance. This deterioration is what we know as “drift.”
When drift occurs, the sensor’s data measurements are no longer reliable and can cause significant damage to the quality of the product and the company’s bottom line.
There is good news; however, thanks to technological advances, most instruments today provide high accuracy, and even though there is still no way drift can be eliminated entirely, calibration can help detect and rectify it.
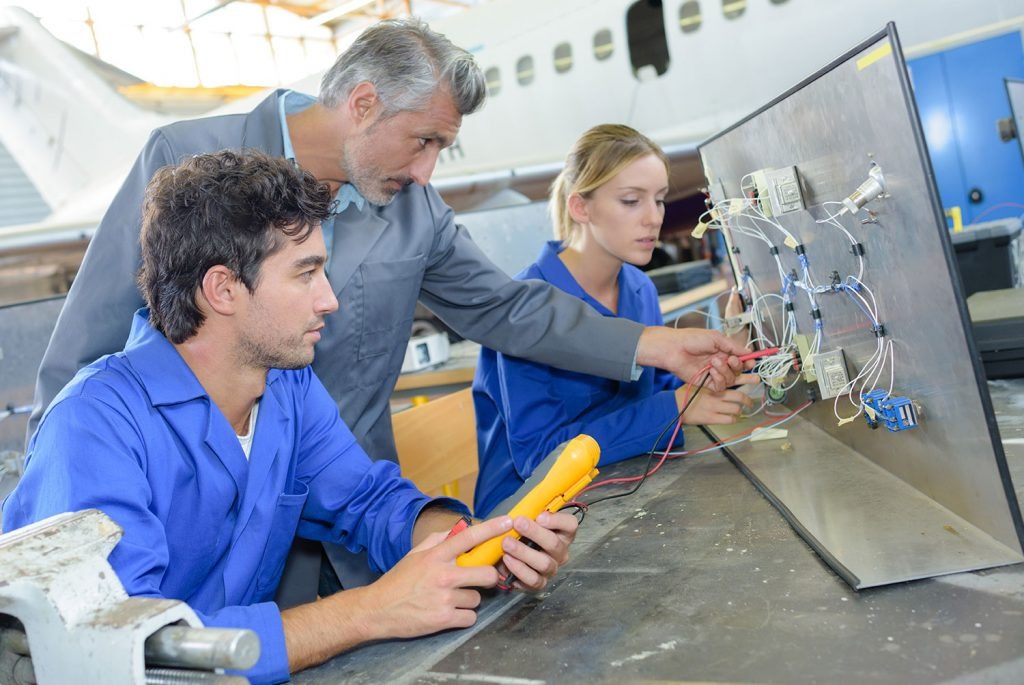
Risks of Not Calibrating Regularly
In times of economic uncertainty, the cost of calibration may push some business owners to neglect or overextend the interval between calibrations. Doing so could cause serious problems.
In an article published in PII Magazine, Jay Lakhani, Senior Applications Engineer, HBM UK, recommends not basing calibration intervals solely on the cost and scheduled downtime of having the instruments tested, calibrated by a certified calibration lab, but to compare that cost to the potential loss due to inaccurate results, more frequent remeasuring, possible recalls, wasted of resources, and probable equipment damage.
Among the many risks associated with not calibrating your instruments regularly, we can list the following:
Product Quality
Inaccurate measurements are bound to affect the manufacturing and production processes, which will generate quality issues in the final product.
Poor quality is a real concern for all businesses, including those in the processed food, pharmaceutical, medical, and petrochemical industries.
Uncalibrated Instruments Can Damage Other Equipment and Harm Employees
Utilizing uncalibrated equipment can lead to unexpected failures that can affect and damage other machine parts and lead to wastage. Additionally, inaccurate measurements can be risky for operators and can lead to severe injuries.
Increase In The Overall Cost and Maintenance
Poorly calibrated and uncalibrated equipment will result in a waste of resources, time, and the workforce.
By regularly providing maintenance and calibration to your equipment, you can effectively reduce downtime, increase performance and reliability, as well as save energy.
Litigation and Fines
Consumer protection laws are in place to ensure that all products sold on the market are safe. As we mentioned before, poorly calibrated equipment can hurt the quality of products manufactured and could potentially lead to negligence claims which carry hefty fines or lawsuits.
To avoid litigation problems and costly fines, ensure you enlist the services of a qualified and reputable calibration lab with ample experience in your industry.
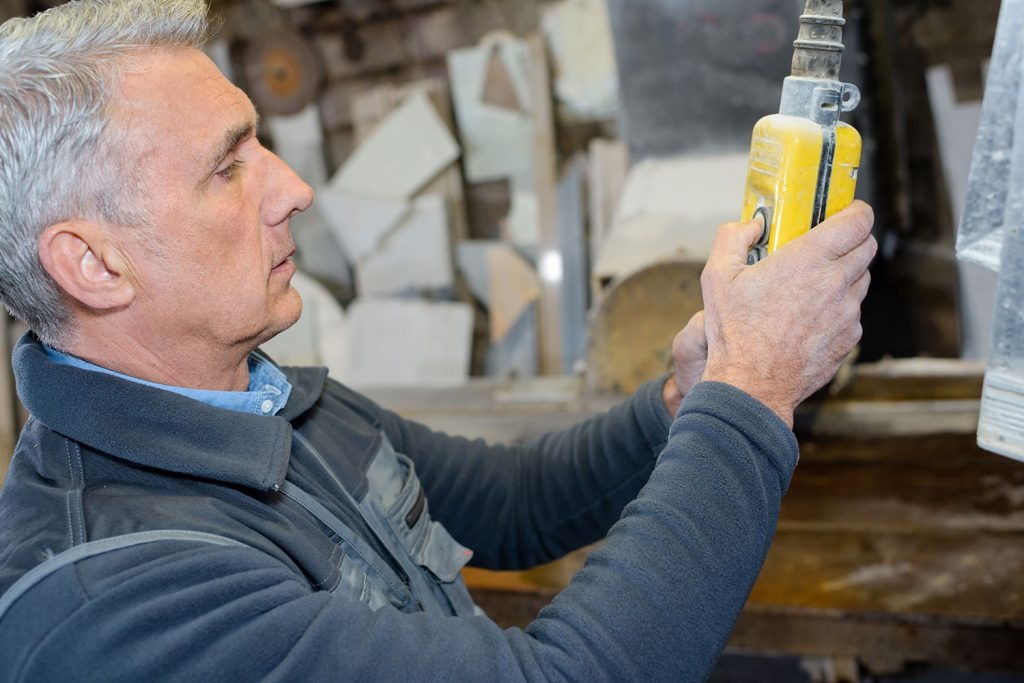
Allometrics Inc.
At Allometrics, we’ve spent the last 40 years helping our customers feel confident that their measurement results are accurate and reliable.
We provide world-class ongoing calibration services to ensure you maximize the performance of your instruments throughout its lifetime.
For more information on our services and capabilities please email us at info@allometrics.com.
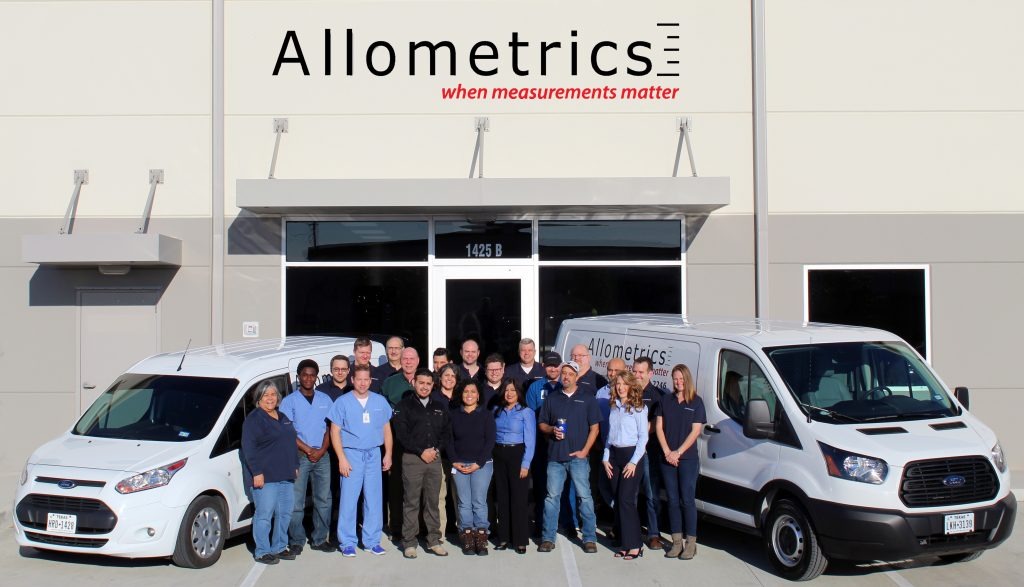